My first Czech engine and its a Turbo Fan.
I don’t speak Russian, I don’t have a manual and I want it running in under 4 weeks – Yikes!
This AI-25 gas turbine engine is originally from a L39 Albatros fighter trainer of Czech origin. The engine has a maximum thrust of about 3500 lbs and weighing in at around 770 lbs. As a twin spool engine the AI-25 should be more fuel efficient and quieter than it’s pure turbo jet cousins.
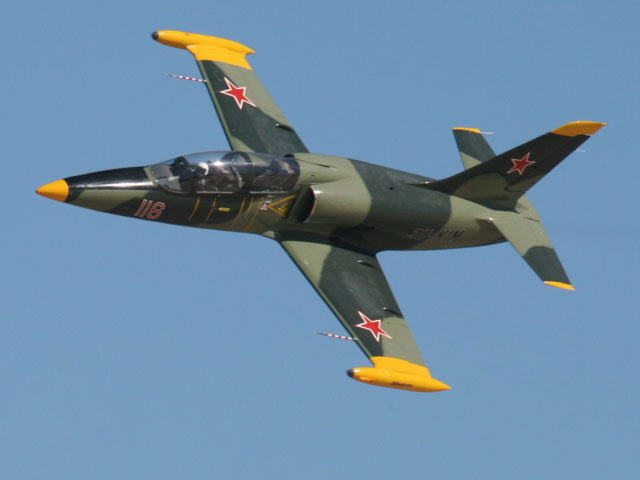
A close up of the compressor guide vanes with the first stage fan just behind them.
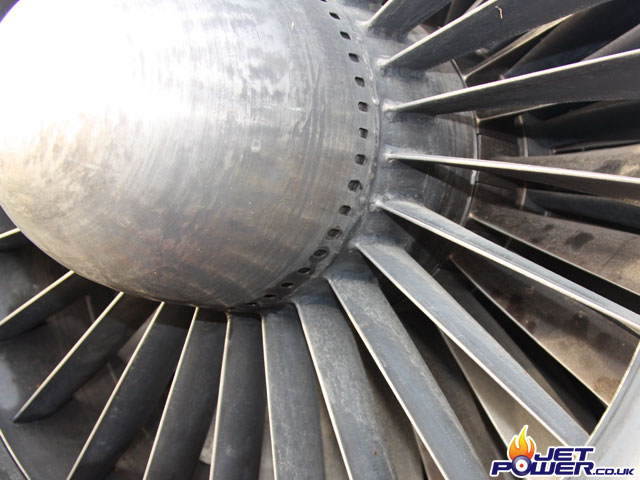
Front view.
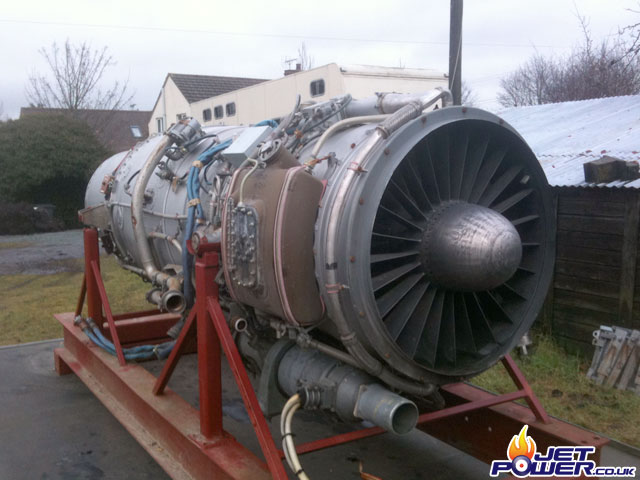
Front view.
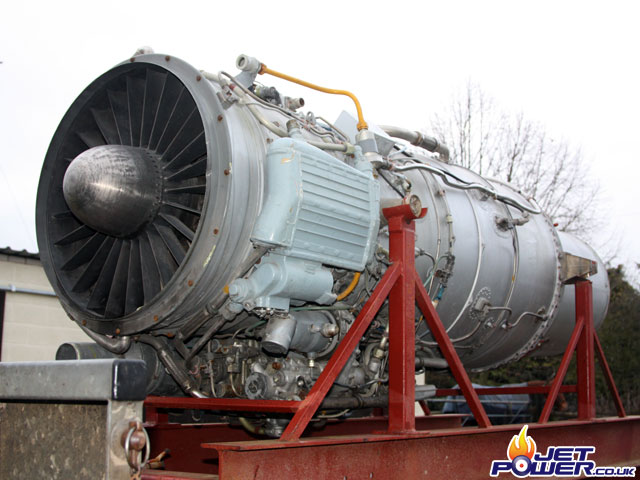
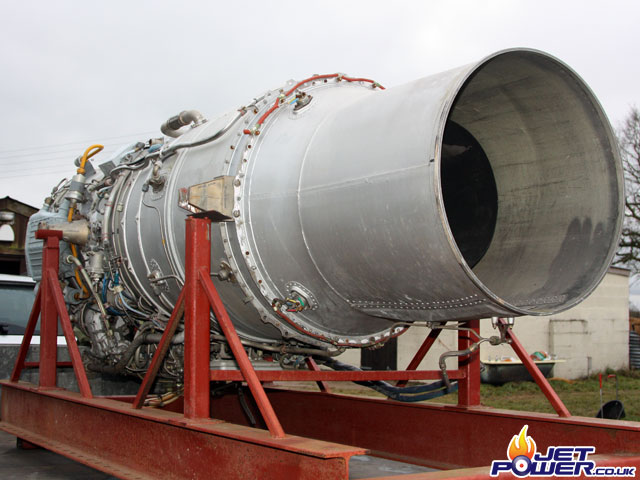
Side rear view.
Side rear view.
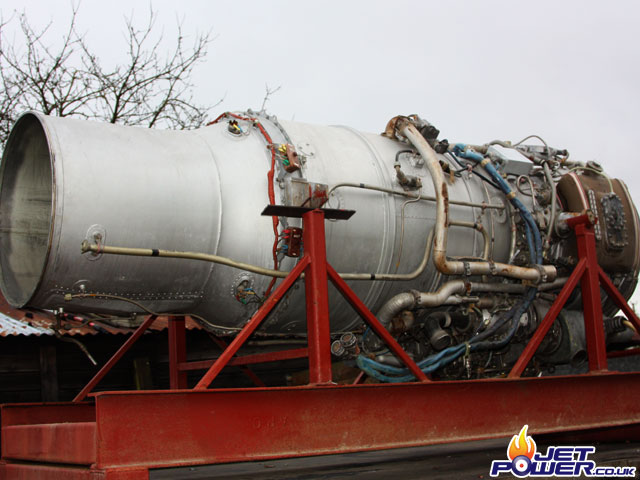
Direct front view.
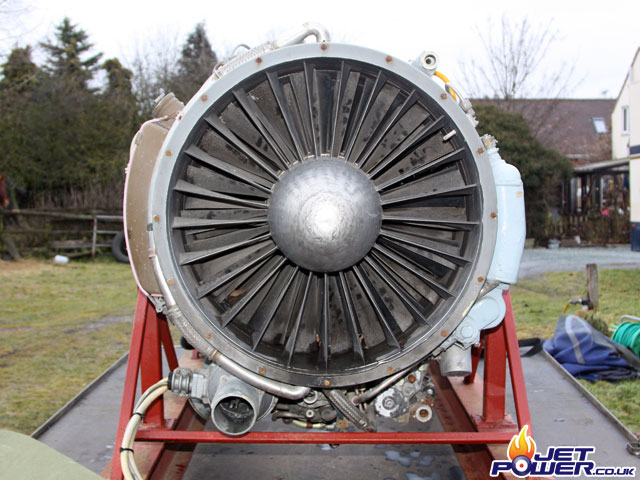
Direct rear view.
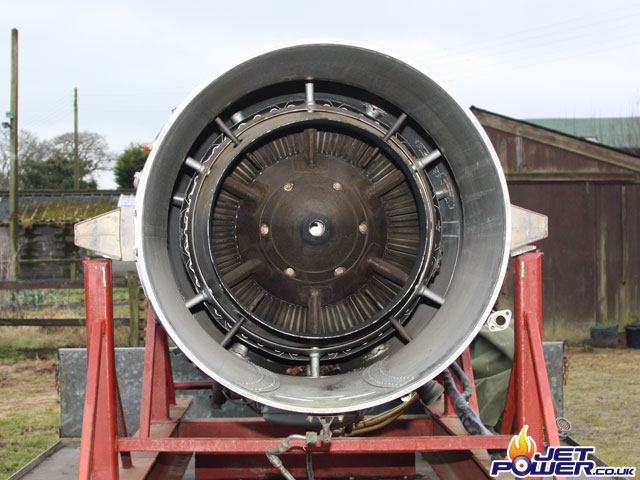
One of the two igniter exciter units.

The engine’s air starter motor is just visible behind the blue multi core cables.

Dual probe k-type thermocouples.
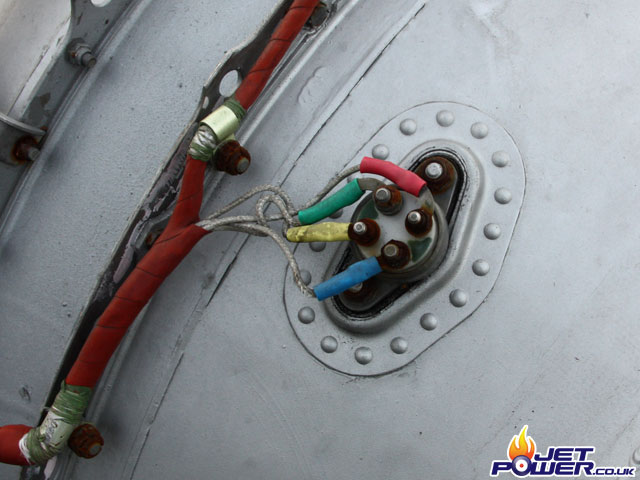
A bit of bad news is that there is a small amount of damage to a hydraulic fitting of some description and the thing that hangs down that is about the size of a coffee cup. I currently have no idea as to what they are for, I just hope they are not important for ground running use only. Also a union is damaged at the bottom of the oil/ fuel heat exchanger.

Conveniently there are some engine lifting lugs fitted so the removal of the red transport frame wasn’t to hard a task.
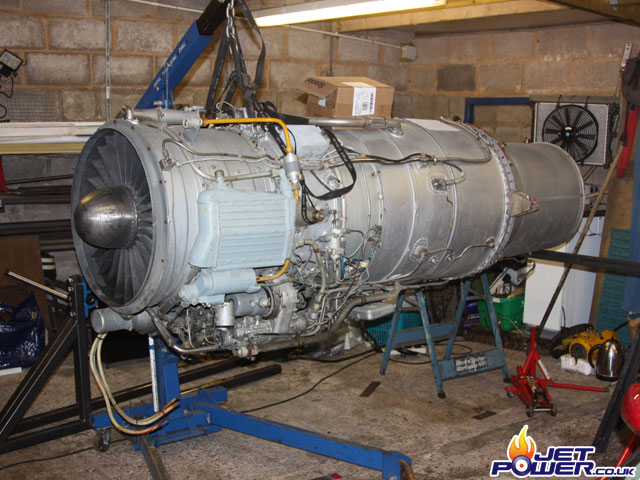
I have designed and fabricated the running/ test frame shown above using 50mm – 5mm wall box section. There are also small castor wheels fitted to allow moving around the workshop, my intention is that they will have no floor contact when they are in a running environment as they are only rated to 100kgs each.
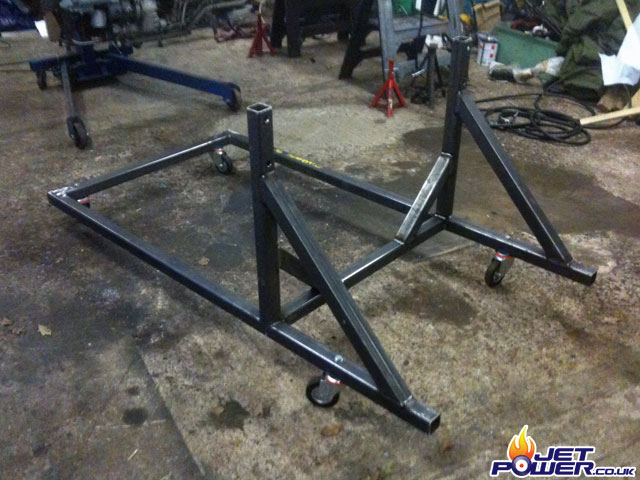
For the main thrust/ pivot mounts of the engine I have decided to use Pillow Block Bearings as they self center which reduces any load on the casing caused my heat expansion or slight discrepancies in the frames dimensions.
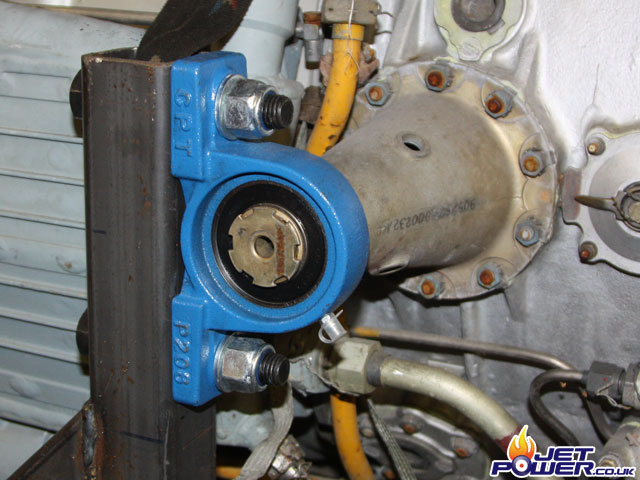
Engine frame fitted, the next job will to fabricate the rear supporting section.

My mate Will helped fabricate the rear brackets, they allow expansion of the engine length and width ways but restrict movement of the engine up and downwards.
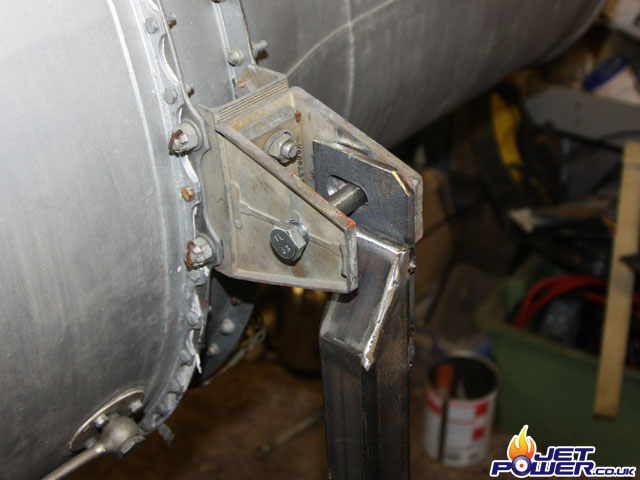
The generator isn’t going to be used currently, so to save space, weight and a little stress on the engine it has been removed, there are no clear markings as to it’s specification.

Freddie Bennett inspecting for FOD.
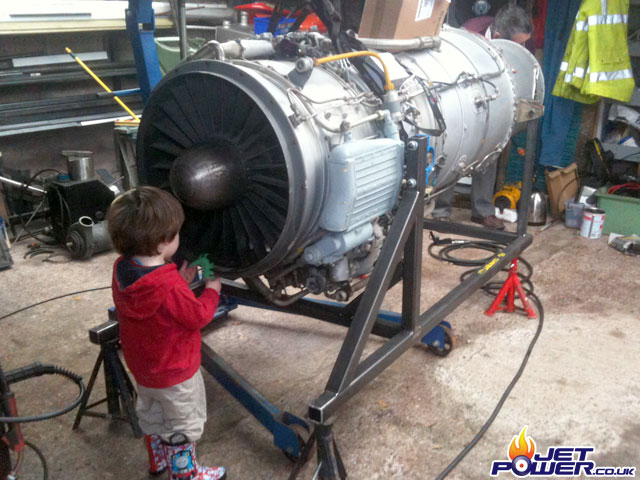
A comment was made that ‘It is Dark in here’,
I have added this to my AI-25 notes.
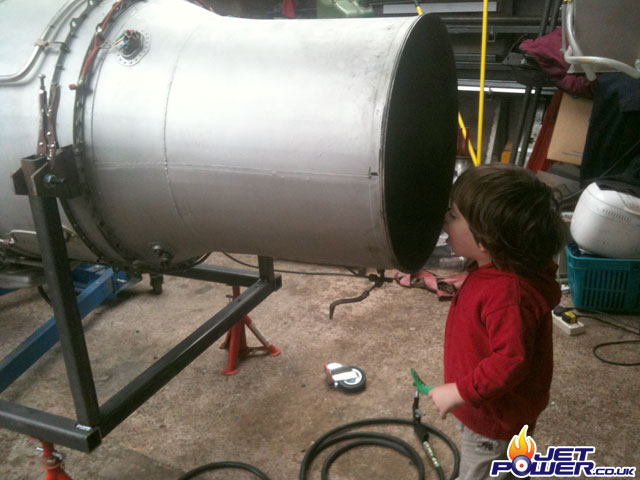
To present the engine in a professional manor I have made a twin axle trailer for transportation, however the engine and frame will be fully detachable from the trailer if required. As pictured all I have to do now is fit the mudguards and make the hitch assembly.
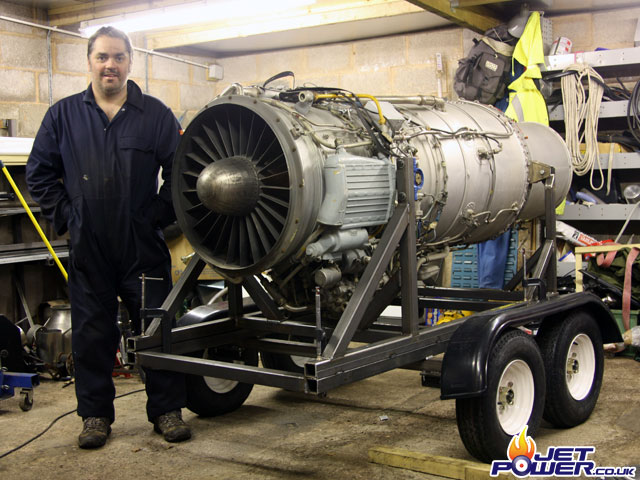
Transport trailer finished bar a coat of paint.
(I may yet tweek it if an idea pops in to my head)
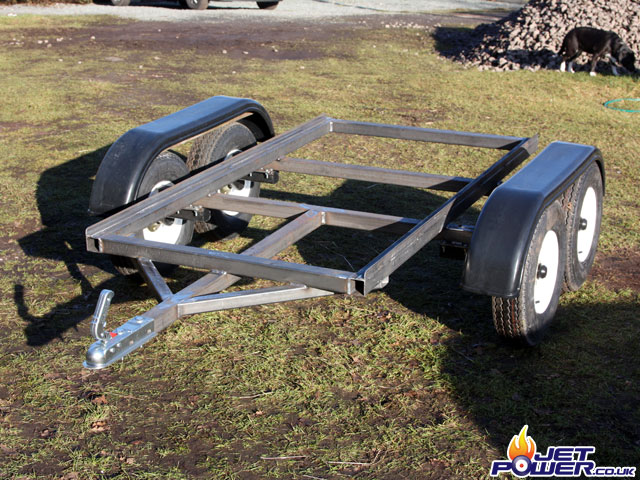
As I stand no chance of getting the mating electrical connectors that match the engines loom (2 x 32 way) I have opted to cut the ends off exposing the individual cables within, they then poke in to a box where they will be terminated in to barrier strips.
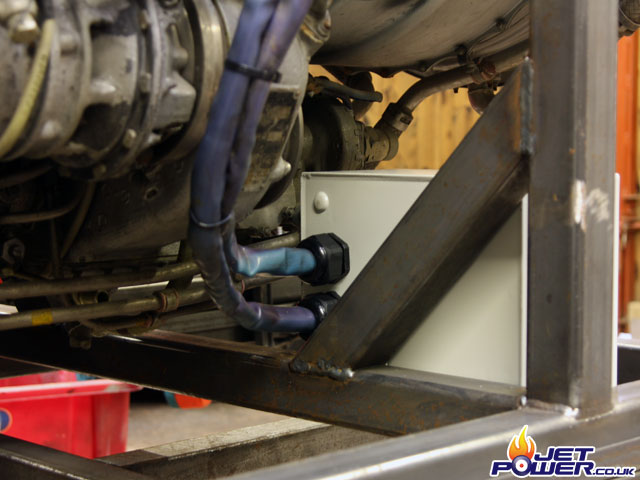
The starboard wiring loom has 32 wires and the port side loom has 22 wires coming from it.
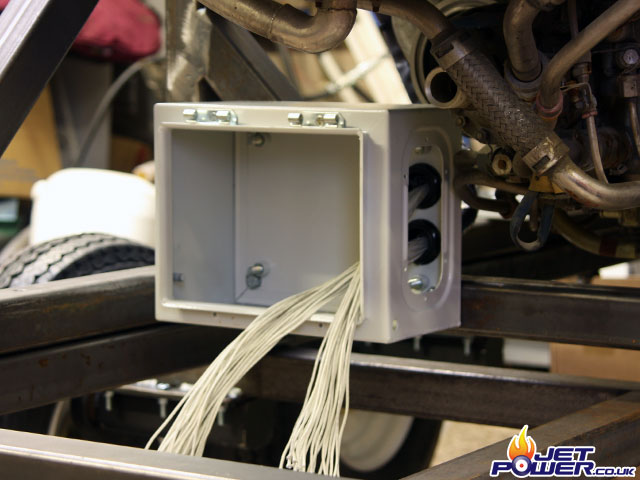
I’m guessing that the above accessory is a hydraulic pump and thus has no use outside of an aircraft, I consequently have concerns about running the pump with zero hydraulic oil flowing though it’s gears. The obvious choice is to remove it like I did with the generator.
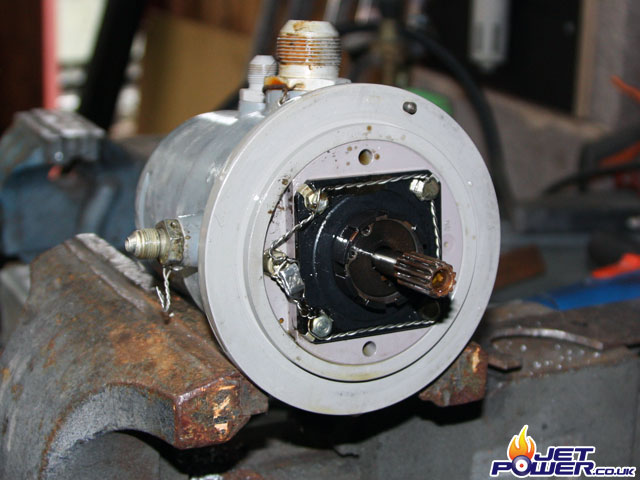
The problem here is that it is required to form a seal to the gearbox, I could make a blanking plate but at the moment I want to avoid extra costs and time issues getting one made. My solution was to remove the quill shaft, which was straight forward and fit the pump back to the engine.
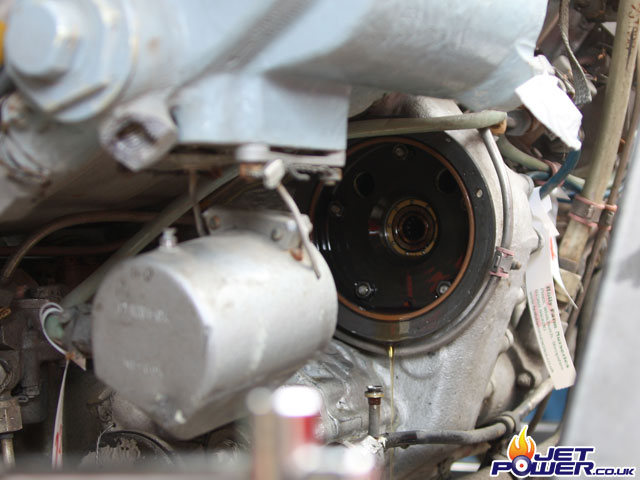
The AI-25 is an air start engine and a hefty supply of compressed air in the region of 0.4 Kg/Sec @ 45 PSI is required, this would usually be produced by a Saphir5 engine and would connect to the AI-25 by the pipe work shown in the photo above.
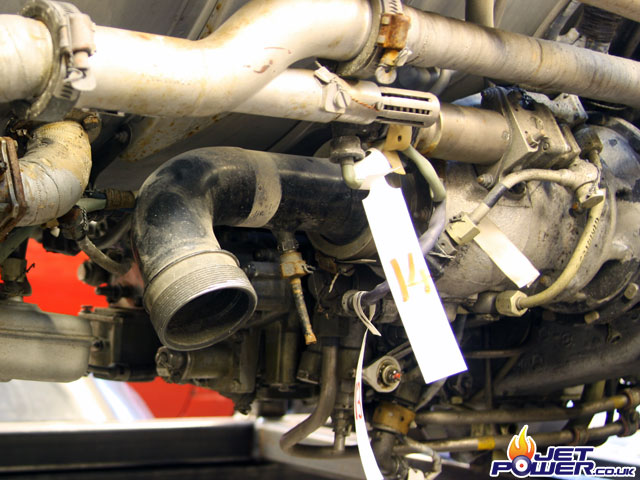
To ease the transportation of the engine and it’s air start unit I have fitted a 2″ instantaneous fire hose fitting to the air starter inlet, a special coupling had to be made to facilitate this. The corresponding male connector will be attached to a length of 2″ fire hose which in turn will connect to the Saphir.
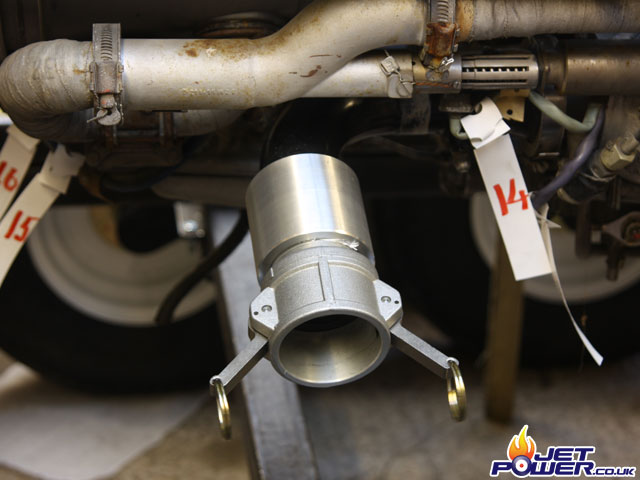
This is the fuel inlet coupling and it happens to be a thread that no one I know has ever heard or seen of before, luckily it did have a fitting on it so at least there’s a chance the thread can be replicated. Just behind the fitting you can see the centrifugal LP fuel pump.
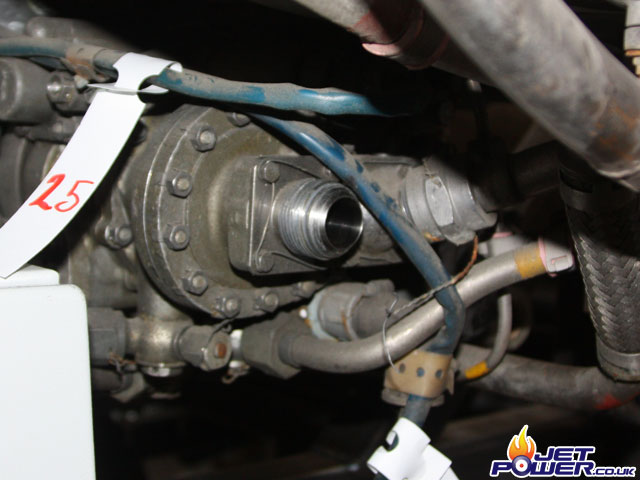
My local engineers (Pete Hunt) adapted the fitting I had so that the input end had a 1″ BSP thread on it, this has made life easier as it is now a standard thread. I have also added a fuel filter capable of 12 gallons per minute with a QR at the end. The engine uses about 1.5 gallons per minute at idle and around 7.5 at full power.
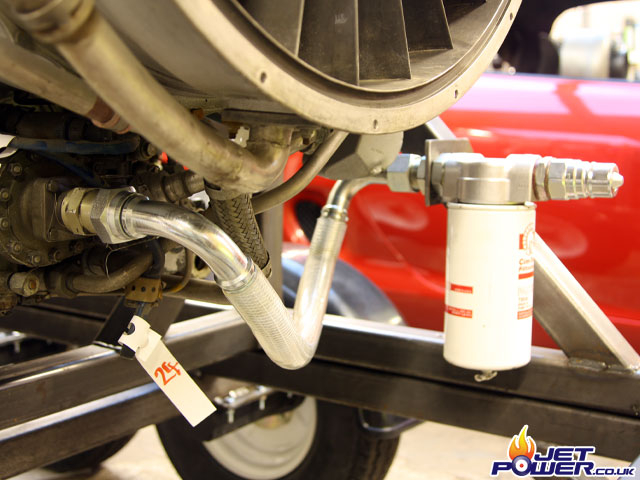
Termination of the tails to 5 barrier strips, the strips facing the camera are the right hand side of the engine and the strips at the bottom are the left hand side. The multi connector has yet to be fitted. Wiring the loom this way makes for excellent electrical troubleshooting.
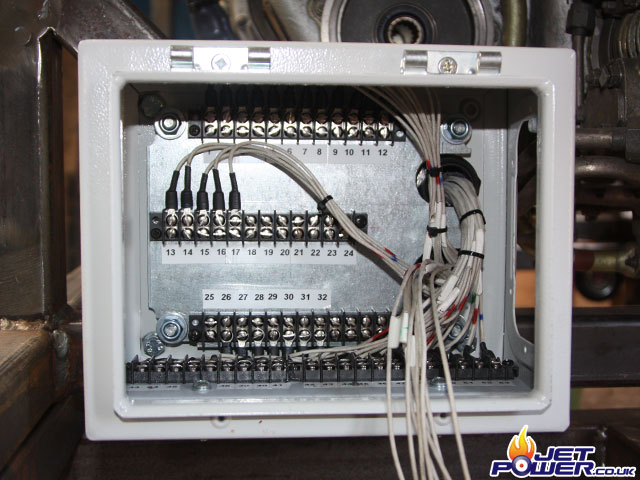
This picture shows the beginning of the control panel, I have resorted to my trusted method of using an ABS short flight case (3U) with an internal tray. Shown fitted are the RPM and EGT gauges.
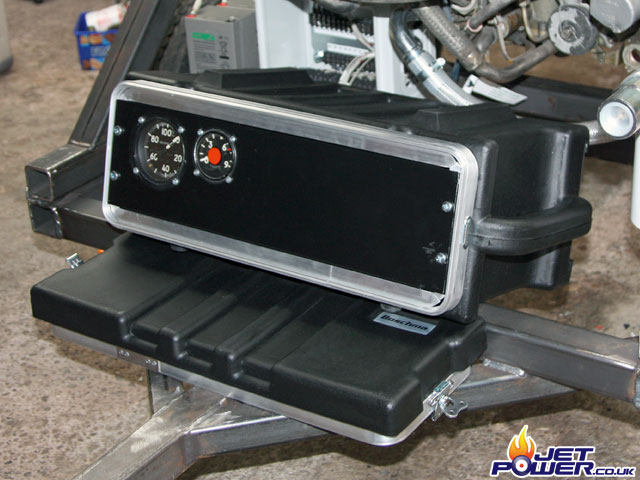
It’s that time for a test run, the interface box has now been wired up to a 50 way QR connector and to this we have wired up the bare essentials. At this point we don’t even know if the engine will run.
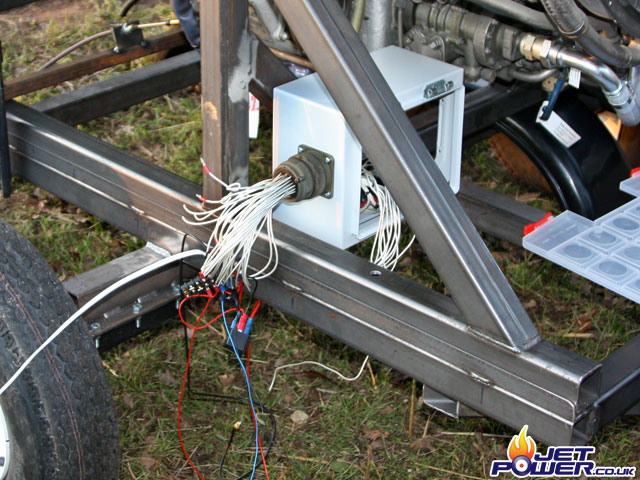
I soon came to the conclusion that the 50mm hose fitting that mated to the engine was going to restrict the air flow to the AI-25’s starter, so I took the decision to use old 70mm fire hose components, these are readily available on ebay and with a bit of machining will fit easily and quickly to the engines. The image above shows the QR connection to the APU starter (Air Producer).
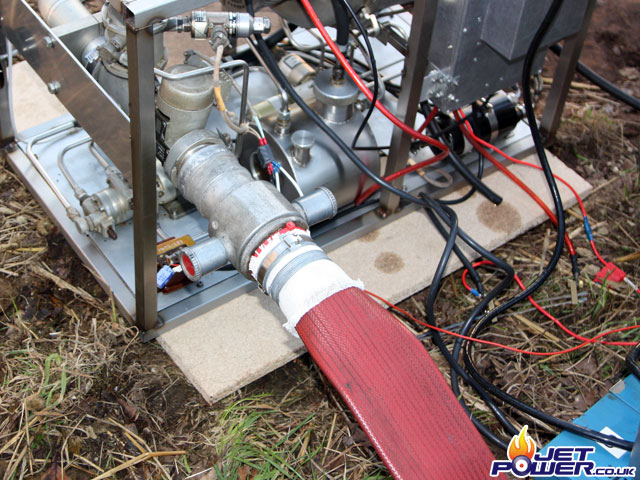
The white cable coming from the engine is the control cable that actuates the air delivery valve on the APU when the start process is initialised, some times known as a wonder lead.
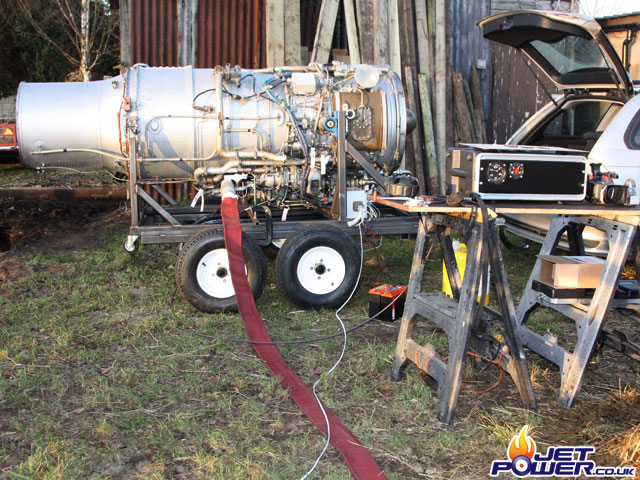
Ian looking confident about the first run.
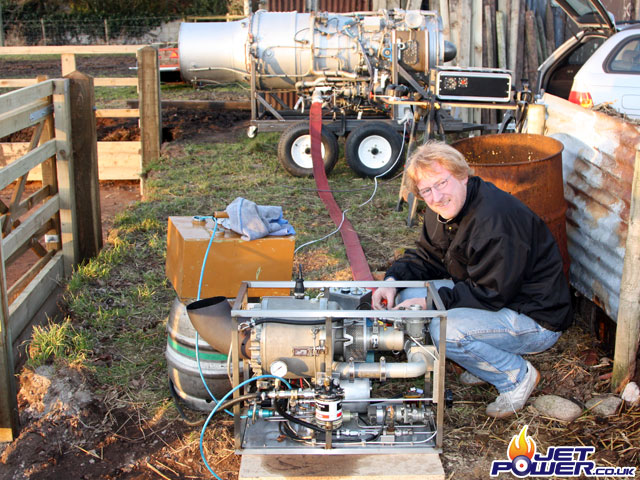
What more can you want, a nice sunset and a jet engine. Video’s of the runs made today can be viewed on the media page, we did have issues with hot starts, but at least it works.
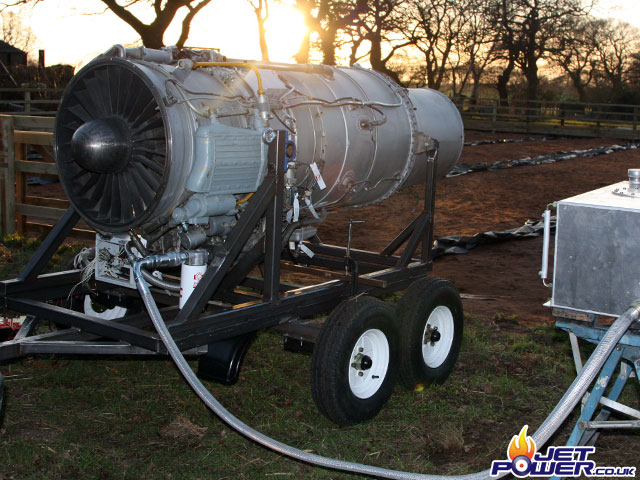
One of the things that may have contributed to the hot starts was that the top air bleed valve was in the open position and at low RPM’s the valves should be closed. This valve was seized and in the open position as pictured.
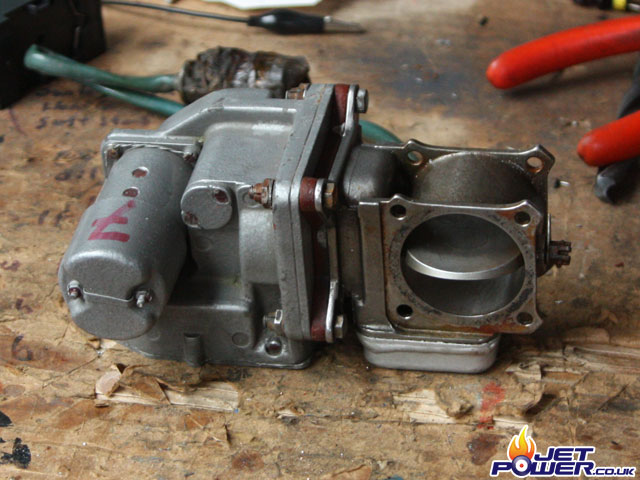
Firstly the motor and reduction gearbox was removed and found to be working well.
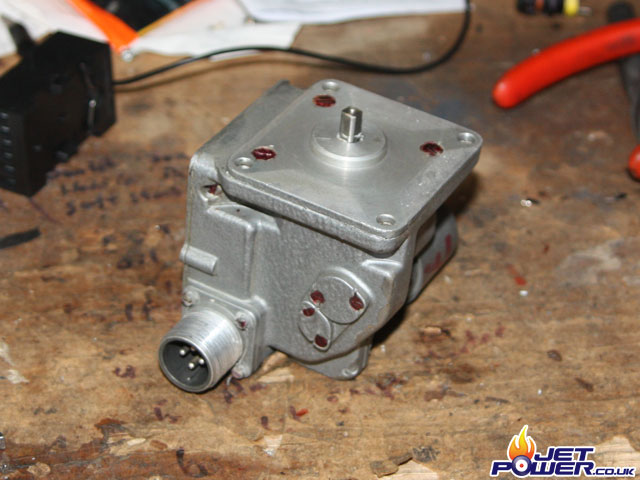
Then I removed the butterfly valve housing and found that it was this part of the assembly that was seized, a bit of tinkering and some WD40 eased it off nicely.
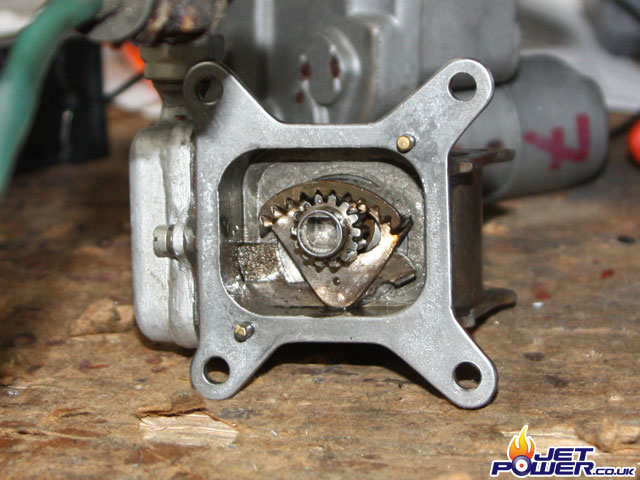
Then I had a think about the valves and made the decision to remove them altogether from the equation, what’s the point of having them if the engines not in a plane? The pipe work was removed, which made the engine look less busy and the surface prepared with some Hylomar.
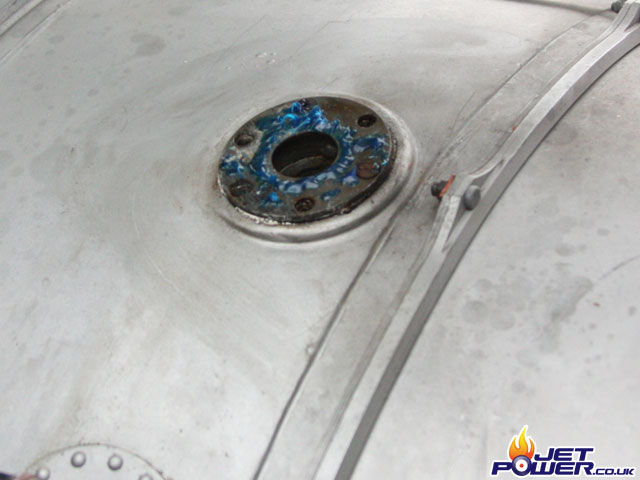
I made disc out of 3mm aluminium and bolted it in to place where the air bleed pipe work used to be.
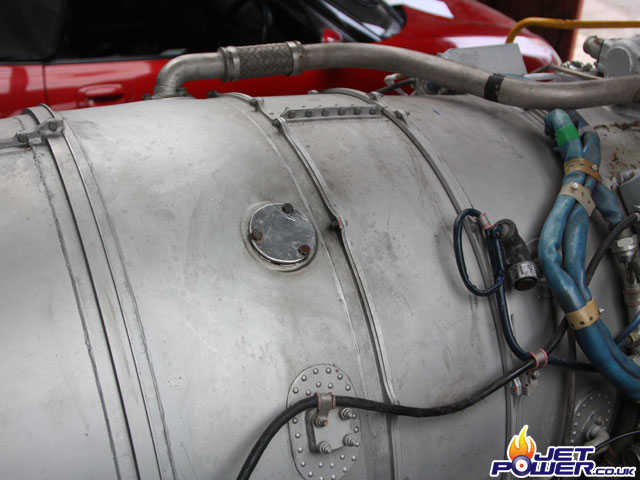
Same again on the underside, I believe this pipe was for the air conditioning, but I may be wrong.
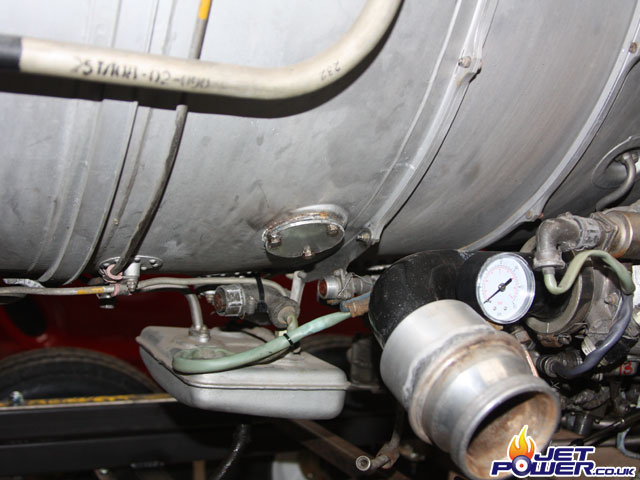
I have been fortunate to have some correspondence with a chap called Bernd Rehn, if you look for anything L39 you will find his name, I believe he is revered as a god in some countries! Based on the bits he has told me and bits I have worked out for myself I have been able to start the final control panel electronics.
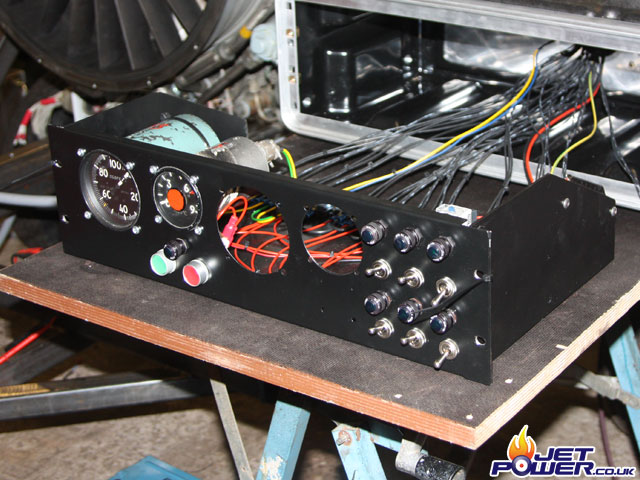
A rear view of the control panel electronics, mainly delay timer relays and normal relays, there are quite a few more components yet to be added.
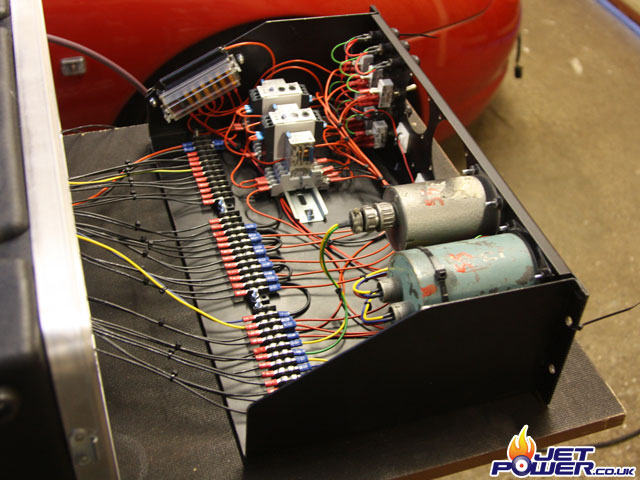
A bit of good news, if you can call it that, is that the damaged device is a differential pressure signaler, basically a device that tells you if your fuel filter is becoming blocked, I believe I can manage with out it as the engine is ground based.
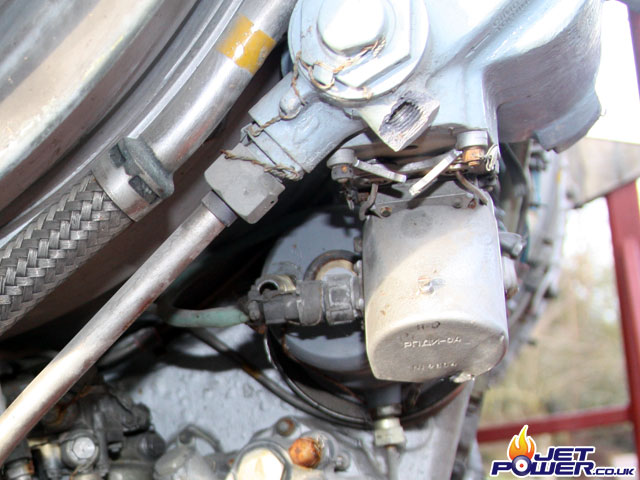
I had the opportunity to try the engine out at a disused airfield, fuel was provided in the form of two 205litre drums of your finest JetA1.
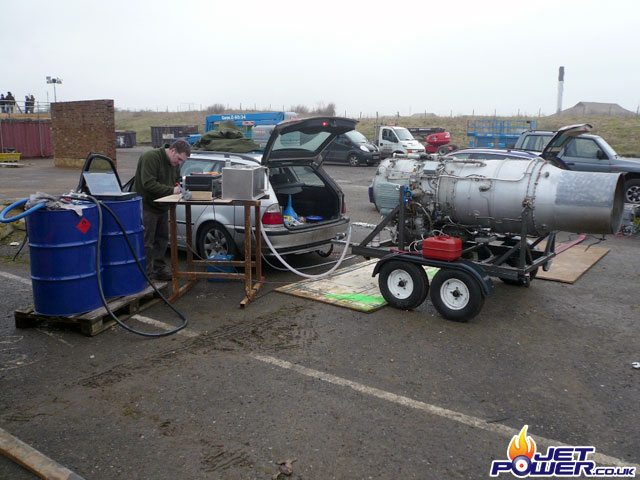
Why didn’t I make one of these before? Using the two RSJ’s from the original transport stand and a few bits of metal that I had lying about, I have made a very useful hoist that is capable of lifting 500KG’s, this makes the removal of the engine from it’s stand a snap and it’s safer as well.

The frame and trailer chassis have been left outside intentionally for a couple of weeks to get a thin layer of rust to form, when this is removed using shot blasting a rough surface remains making the adhesion of the powder coating stronger.
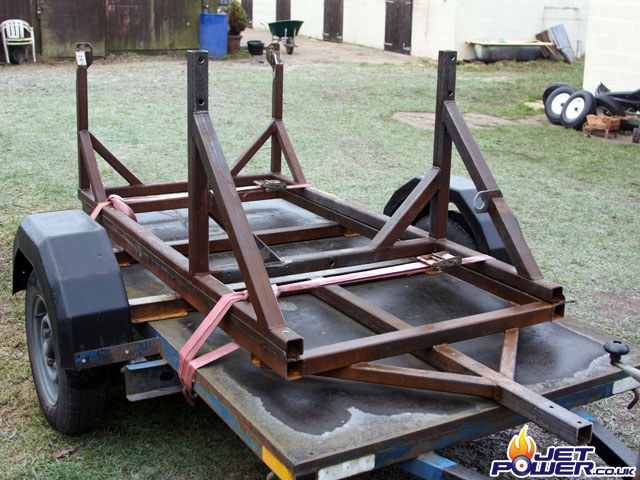
The trailer has now been powder coated and is ready to be put back on the engine, nice to see metal without brush strokes in it.

The engine about to be reattached to the frame.

The image shows the control panel from the rear, almost complete apart from a 400Hz, 48volt inverter which has yet to be made.
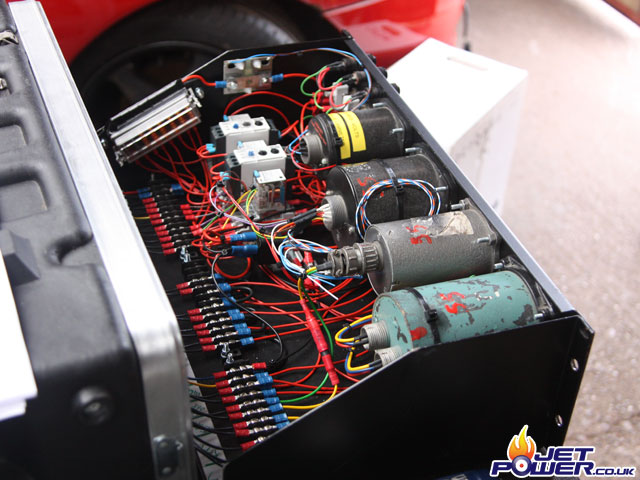
Front view showing the gauges and control switch’s. Dual RPM, EGT, Oil Pressure, Oil Temp, Fuel Pressure, Volt Meter and an Ammeter.
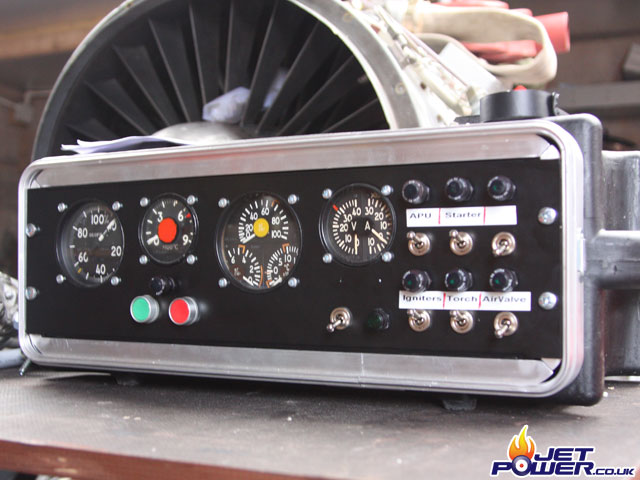